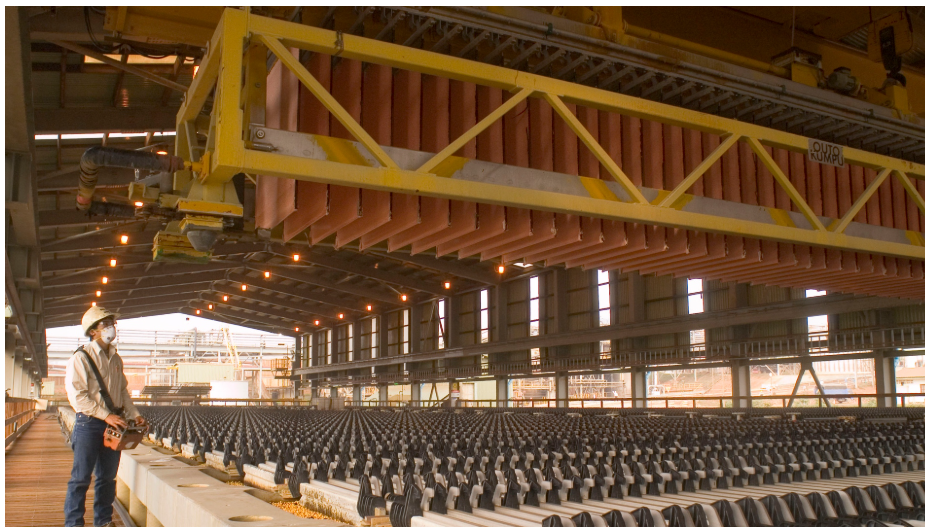
In the heart of Papua Province’s remote Sudirman Mountain Range, PT Freeport Indonesia (PTFI) operates as a key affiliate of Freeport-McMoRan (FCX) and MIND ID Indonesia’s Mining Industry, extracting copper, gold, and silver from the region’s rich ores. Situated at elevations of 2,800-2,900 meters above sea level, PTFI’s Mill Facility processes a staggering 200,000 to 250,000 tons of ore daily. For over two decades, Drimax 1234 has been instrumental in their dewatering processes. However, BASF Indonesia’s innovative sustainability initiative is now transforming this aspect of mining operations. By transitioning from Drimax 1234 to the safer and more cost-effective Drimax 1239NF, contained in Isotank rather than Intermediate Bulk Containers (IBCs), BASF Indonesia aims to overcome logistical constraints, environmental challenges and product integrity concerns associated with IBC usage in PTFI. This strategic shift not only enhances operational efficiency and reduces environmental impact but also emphasizes BASF’s and PTFI’s commitment to sustainable mining practices in the unique terrain of lowlands and highlands in Mimika, Papua.
PTFI has been using Drimax 1239NF since last year as a replacement for Drimax 1234. Unlike its predecessor, Drimax 1239NF falls under the category of non-DG material (non-flammable), thereby offering PTFI advantages in terms of safety and handling. In addition, Drimax 1239NF offers comparable performance to Drimax 1234 but at a lower cost, making it more cost-effective.
Firstly, the primary objective of utilizing Drimax 1239NF is to reduce the cake moisture of vacuum filtration so that it can comply with the Transportable Moisture Limit for shipment. Additionally, the use of Drimax 1239NF indirectly leads to reduced fuel consumption in downstream filtration processes i.e., rotary kiln dryers.
Secondly, PTFI is currently conducting trials with Drimax 1239NF in its pressure filter, and preliminary results indicate an increased feed rate, thereby enhancing process productivity. Increasing the productivity of the pressure filter can be used to reduce the load of the vacuum filter circuit (rotary disc filter followed by rotary kiln drier) which leads to a reduction of fuel usage of the drier.
Switching the packaging of Drimax 1239NF from IBC to Isotank will result in reduced waste of IBC tote and as well as easier handling.
For years, PTFI has relied on IBCs for the transportation and storage of various chemicals, including the essential Drimax. However, the limitations inherent to IBCs have prompted a re-evaluation of the suitability for PTFI’s diverse operational terrain:
- Capacity and Efficiency Constraints: With an average consumption of 400 IBCs annually, PTFI encounters logistical hurdles due to the limited storage capacity of IBCs. Frequent transportation requirements not only strain resources but also contribute to increased energy consumption and carbon emissions.
- Environmental Impact: The predominance of plastic in IBC construction poses environmental challenges, with disposal and recycling presenting significant hurdles. As plastic waste continues to be a global concern, the reliance on IBCs exacerbates PTFI’s ecological footprint.
- Product Integrity and Waste Management: Maintaining the purity of chemical products during transportation is paramount for PTFI’s operations. However, the design of IBCs often leads to product contamination, while residual chemicals left in the containers contribute to waste and potential environmental hazards.
To address these challenges, BASF suggests to PTFI to use Isotank as a sustainable alternative to IBCs. This transition is reinforced by several key advantages tailored to the unique operational landscape of Mimika, Papua:
- Enhanced Capacity and Operational Efficiency: Isotank offers significantly larger storage capacities compared to IBCs, reducing the frequency of transportation requirements. This optimization streamlines logistical operations across PTFI’s expansive operational area in lowland regions.
- Reusable and Recyclable Design: Isotank is designed for multiple-use cycles, minimizing the need for constant manufacturing and reducing resource consumption. Their metal construction facilitates easier recycling, aligning with PTFI’s commitment to sustainable practices.
- Reduced Environmental Footprint: By transitioning to Isotank, PTFI is actively reducing its reliance on single-use plastics, thereby contributing to a reduction in plastic waste. Moreover, the sturdier construction of the Isotank minimizes the risk of chemical spillage, enhancing environmental safety standards.
In conclusion, the collaborative efforts between BASF Indonesia and PT Freeport Indonesia mark a significant stride towards sustainable mining practices in the challenging terrain of Mimika, Papua. Through the adoption of Drimax 1239NF and the transition from IBCs to Isotank, PTFI enhances operational efficiency and addresses critical environmental concerns. The strategic shift highlights a commitment to reducing carbon emissions, minimizing plastic waste, and ensuring the integrity of chemical products vital for mining operations. Moreover, the successful implementation of these innovations not only optimizes resource utilization but also sets a target for responsible mining practices, aligning with global sustainability goals. As PTFI continues to establish advancements in the mining sector, this partnership with BASF serves as an indication of the transformative power of sustainable solutions in the pursuit of environmental stewardship and operational excellence.
Article Credit: basf